個別のカスタマイズやお客様の声など、実際に導入した事例についてご紹介いたします。
コイル測定データを自動で記録・計算・解析導入による品質管理業務向上 |
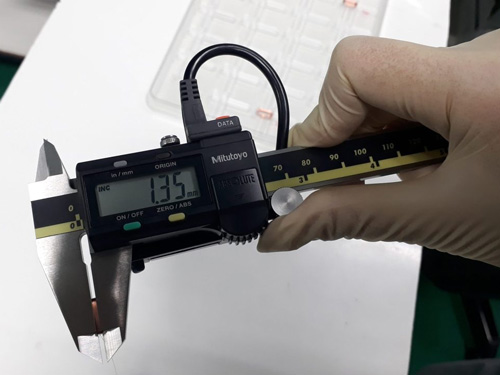
| 検査成績表を手で作成する際、誤記や読みにくいというお客様の声を反映して、QCプロという自動測定ソフトウェアを導入することになりました。この改善により、コイルの検査成績表の作成時間が大幅に短縮され、品質管理業務の向上も実現しました。
●
| 品質管理業務の向上
| ●
| 検索機能よりトレーサビリティしやすい管理
| ●
| お客様への正確な検査成績表を提供
|
|
▲ PAGE TOP
一貫生産体制による品質安定化(モールドコイル) |
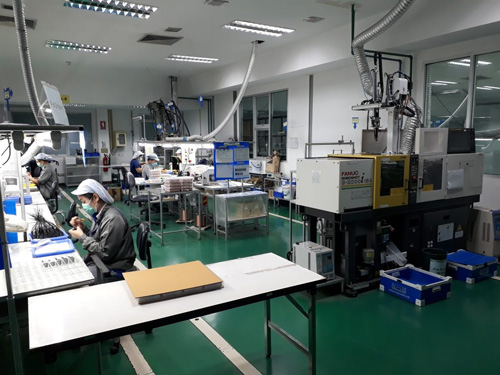
| 工程毎に複数社に分散していた製品を弊社にて一貫生産体制を構築することで品質の安定化を実現しました。汎用巻線機をベースに各部改造を行い、各工程のタクトバランスを調整した上で成型、巻線、組立、オーバーモールド工程を1つのラインに集約しているため、仕掛在庫を抑制しつつ生産性を大きく向上しています。
●
| 工程・品質の安定
| ●
| トラブル発生時の責任の明確化、調査・対策のスピード向上
| ●
| 納期の短縮
|
|
▲ PAGE TOP
小型トランス2次巻線の多軸多数個取りによる生産能力向上 |
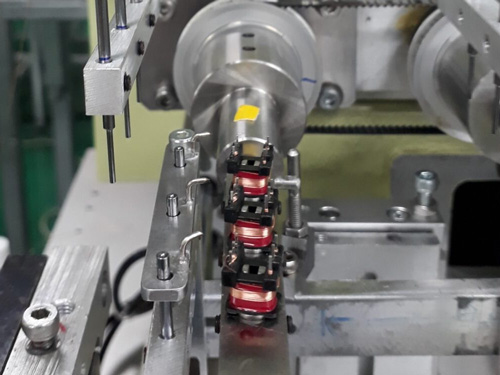
| お客様の要求数量増加に対応するため、単軸巻線機で製造していた小型トランスの2次巻線工程をPRONECでは実績の多い多軸巻線機による多数個取りとすることで150Kpcs/月から300Kpcs/月へ大幅に生産能力を向上しました。この改善により生産ラインの人員追加をすることなく増産依頼に対応することが可能となりました。
●
| 生産能力の向上
| ●
| ボビン位置精度の向上による不良の削減
| ●
| 作業者の手作業が減ることで品質改善
|
|
▲ PAGE TOP
特性検査・試験工程の作業効率改善 |
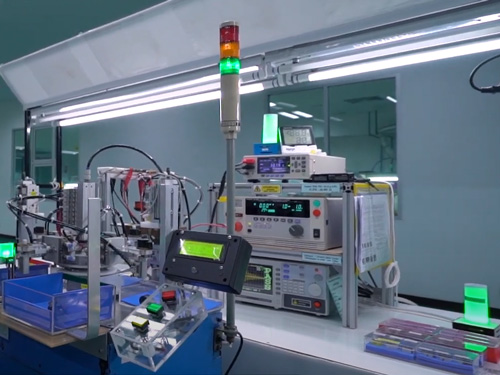
| お客様の要求数量増加に対応するため、特性検査・試験工程の作業効率化に取り組みました。従来は抵抗検査、耐電圧試験、絶縁抵抗試験、インパルス試験と4つの検査・試験工程をそれぞれ別々に行っておりましたが、プローブを共通化し検査機の切り替え、製品の排出までをシステム化することで作業効率を大幅に改善しました。測定結果がOKの場合自動で製品を排出し、NGの場合は専用のBOXに排出するように制御しています。
●
| 生産能力向上
| ●
| 手作業による測定条件のバラつき防止
| ●
| 目視による検査結果の見落とし防止
|
●
| システム全体の定期的な点検が必要
| ●
| 対応できる製品形状に制限がある
|
|
▲ PAGE TOP
多軸巻線機の多数個取りによる生産能力向上 |
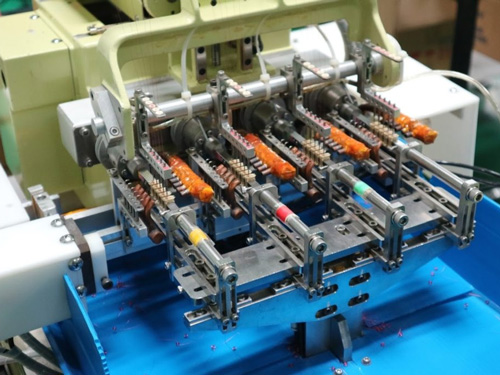
| 月数百万個の製品をイニシャル費用を抑えて安定的に量産化するため、通常1軸で1個の巻線を行う多軸巻線機を社内で改良し、1軸5個の多数個取りを実現しました。品質安定までに半年の時間を要しましたが、設備1台あたりの生産能力が飛躍的に向上しました。この生産方式は生産能力と引き換えに段取り時間が増加するものの、一定数以上の生産数量がある場合には大きなコストメリットが得られます。
●
| 取り数の増加による生産能力の向上
| ●
| イニシャルコストの削減
| ●
| スペースの削減
|
●
| 段取り時間の増加
| ●
| 治具の複雑化、高精度化
| ●
| 対応できる形状や仕様に制限がある
|
|
▲ PAGE TOP
自社製自動半田装置による品質安定化 (半田ボール低減、半田レベル安定) |
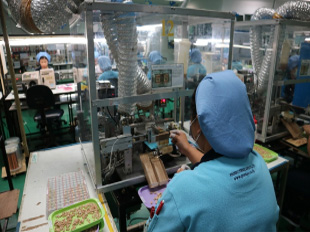
| 数十ミクロン単位の半田レベル管理と半田ボール飛散防止のため、自動半田装置(ロータリー式、アーム式)を開発し品質の安定化を実現しました。過去の実績から 不具合に対して考えうる対策を全て盛り込むことで半田ボールの飛散を低減しています。
●
| 半田品質の安定化
| ●
| 作業、検査工程の削減
| ●
| 歩留りの向上
|
●
| 対象の製品に合わせて一部改造が必要(イニシャル費が発生)
| ●
| 大量生産向き(月産200Kpcs~)
|
|
▲ PAGE TOP