บริษัทฯขอยกตัวอย่างการปรับปรุงซึ่งตอบสนองต่อลูกค้าเฉพาะกลุ่ม และเสียงตอบรับของลูกค้า
ปรับปรุงงานด้านการควบคุมคุณภาพซึ่งเกี่ยวกับการวัดคอยล์ โดยใช้ระบบอัตโนมัติ ทั้งการบันทึก การคำนวนผล และการวิเคราะห์
|
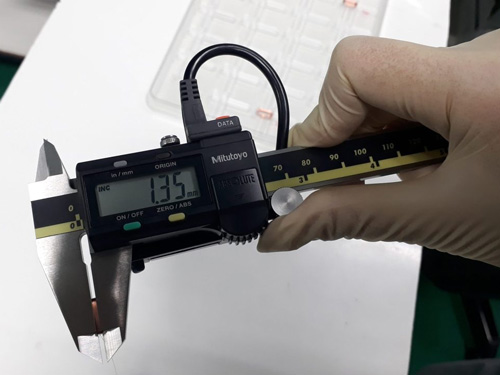
|
บริษัทฯได้รับ feed back จากลูกค้าว่าการวัดและการบันทึกข้อมูลด้านมิติของคอยล์ด้วยมือนั้น ตอนอ่านค่าการวัดเป็นไปอย่างยาก อาจจะเกิดการผิดพลาด ดังนั้นเราจึงจัดหา software ด้านการวัดแบบอัตโนมัติ ชื่อ QC Pro มาใช้งาน การปรับปรุงนี้ทำให้ลดเวลาในการวัดและการเขียนรายงานได้อย่างมีนัยสำคัญ และสามารถปรับปรุงการทำงานด้านการควบคุมคุณภาพ
●
|
สามารถปรับปรุงการทำงานด้านการควบคุมคุณภาพ
|
●
|
การตรวจสอบย้อนกลับและการควบคุมง่ายขึ้น และดีกว่าการค้นหาผลการวัดแบบเดิม
|
●
|
สามารถจัดทำรายงานผลการตรวจสอบที่มีความแม่นยำยิ่งขึ้นให้กับลูกค้า
|
●
|
จำเป็นต้องจัดระบบการตรวจสอบอย่างสม่ำเสมอ
|
|
▲ PAGE TOP
รักษาคุณภาพให้มีคงที่ด้วยระบบการผลิตแบบบูรณาการ
(การฉีดพลาสติกครอบคอยล์)
|
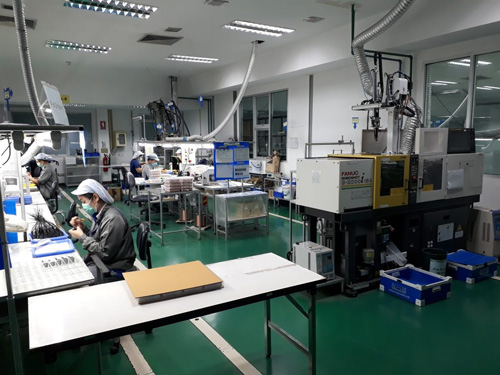
|
บริษัทฯสามารถจัดสรรและบูรณาการการผลิตให้มีความหลากหลายและทำให้เกิดความมีเสถียรภาพด้านคุณภาพ เราสามารถจัดวางโครงสร้างสายการผลิตให้เป็น1ไลน์นับจากเครื่องพันคอยล์เอนกประสงค์ การจัดสมดูลเวลาของการผลิต การฉีดขึ้นรูปพลาสติก(สำหรับคอยล์โมเดลที่ต้องฉีดพลาสติกครอบคอยล์) การพันคอยล์ การประกอบ การฉีดพลาสติกครอบคอยล์ จึงสามารถควบคุมสต๊อคและปรับปรุงผลิตภาพในกระบวนการผลิตด้วยดี
●
|
เกิดเสถียรภาพของกระบวนการผลิต และคุณภาพ
|
●
|
สร้างความชัดเจนในหน้าที่ความรับผิดชอบยามเกิดปัญหา
วิเคราะห์และสร้างมาตรการปรับปรุงแก้ไขได้อย่างรวดเร็ว
|
●
|
ลดเวลาการส่งมอบ
|
|
▲ PAGE TOP
ปรับปรุงกำลังการผลิตTransformerขนาดเล็กแบบพัน 2 ขั้นตอนโดยใช้เครื่องจักรแบบหลายแกน
|
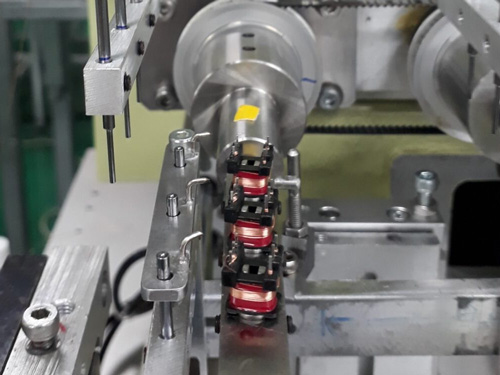
|
เพื่อตอบสนองความการของลูกค้าที่มีมากขึ้น ในส่วนของ Transformer ขนาดเล็กที่ต้องใช้การพันคอยล์ขนาดเล็กครั้งที่ 2 จากการใช้เครื่องพันคอยล์แบบแกนเดี่ยว มาเป็นแบบหลายแกน PRONEC จึงสามารถเพิ่มกำลังการผลิตจาก เดือนละ 150 Kpcs เป็นเดือนละ 300 Kpcs ซึ่งการปรับปรุงกำลังการผลิตนี้สามารถทำได้โดยไม่ต้องเพิ่มกำลังคนในการผลิต
●
|
เพิ่มกำลังการผลิต
|
●
|
ลดของเสียที่สาเหตุเกิดจากตำแหน่งของ Bobbin ไม่ตรงจุด
|
●
|
สามารถปรับปรุงคุณภาพจากการลดการใช้พนักงานในการผลิต
|
●
|
ปรับปรุงเวลาในการ Set up เมื่อเริ่มการผลิตใหม่
|
|
▲ PAGE TOP
ปรับปรุงประสิทธิภาพงานด้านกระบวนการทดสอบ การตรวจสอบ คุณลักษณะเฉพาะของผลิตภัณฑ์
|
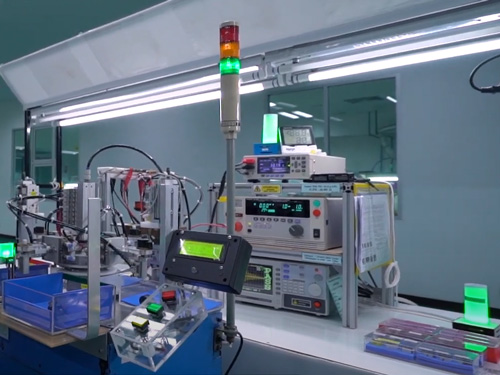
|
เพื่อตอบสนองต่อความต้องการของลูกค้าในด้านการเพิ่มผลผลิต บริษัทฯได้ทำการปรับปรุงประสิทธิภาพของกระบวนการทดสอบ การตรวจสอบคุณลักษณะเฉพาะของผลิตภัณฑ์ โดยในอดีตการทดสอบ หรือการทดสอบ เป็นแบบแยกทำทีละขั้นตอนตาม Probe ที่แตกต่างกันของเครื่องมือวัดแต่ละประเภท เช่น resistance inspection, withstand voltage test, insulation resistance test, และ impulse test ดังนั้นจึงได้สร้าง Probe และระบบที่เกี่ยวข้องซึ่งสามารถใช้ทดสอบและตรวจสอบผลิตภัณฑ์ร่วมในครั้งเดียว ด้วยการนำชิ้นงานที่ต้องทดสอบและตรวจสอบเข้าไปใน Probe และระบบที่ได้ปรับปรุงขึ้นมา หลังจากนั้นเครื่องทดสอบและตรวจสอบจะทำงานที่ละขั้นตอนโดยอัตโนมัติตั้งแต่ขั้นตอนแรกจนถึงการแสดงผลการทดสอบและการตรวจสอบโดยไม่ต้องสิ้นเปลืองเวลาในการแยกหรือการเปลี่ยน Probe ทั้งนี้ถือว่าเป็นการปรับปรุงประสิทธิภาพที่ดีขึ้นเป็นอย่างมาก หากเครื่องแสดงผลการทดสอบและตรวจสอบผ่าน (OK) ชิ้นงานดังกล่าว จะถูกนำไปสู่ขั้นตอนต่อไป แต่หากว่าเครื่องแสดงผลการทดสอบและตรวจสอบไม่ผ่าน (NG) ชิ้นงานดังกล่าวจะถูกควบคุมแยกออกมาใส่ลง BOX ที่กำหนดไว้เฉพาะ
●
|
เพิ่มกำลังการผลิต
|
●
|
ป้องกันการผิดเพี้ยนของในการวัด อันเกิดจากการทำงานแบบแมนนวน
|
●
|
ป้องกันการผิดพลาดของการใช้สายตามองเพื่อแยกงานดีและงานเสีย
|
●
|
การตรวจยืนยันในความเที่ยงตรงของระบบโดยรวมตามความเหมาะสมถือว่าเป็นสิ่งจำเป็น
|
●
|
มีข้อจำกัดที่เกี่ยวข้องการลักษณะรูปร่างของชิ้นงานที่จะตรวจ
|
|
▲ PAGE TOP
ปรับปรุงกำลังการผลิตโดยการใช้เครื่องจักรพันคอยล์แบบหลายแกนหลายชิ้น
|
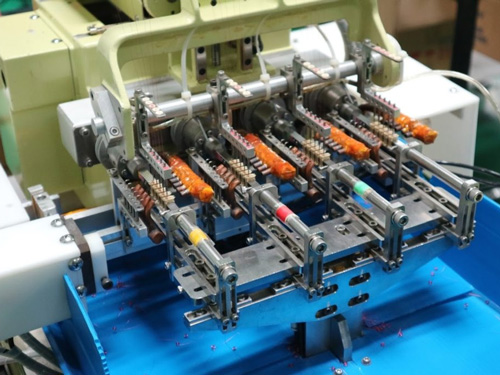
|
เพื่อควบคุมความเสถียรของต้นทุนขั้นต้นในการผลิตแมสโปรดักชั่นจำนวนล้านชิ้นในแต่ละเดือน บริษัทฯได้ใช้เวลากว่าครึ่งปีปรับปรุงเครื่องจักรพันคอยล์แบบหลากแกนให้คุณภาพเสถียนจนสามารถพันคอยล์ได้แกนละ 5 ชิ้น จากปกติซึ่งเป็นแบบแกนเดี่ยวซึ่งพันคอยล์ได้ครั้งละ1ชิ้น ถือเป็นการเพิ่มประสิทธิภาพการผลิตอย่างก้าวกระโดด ถึงแม้นว่าการใช้เวลาเตรียมระบบการผลิตนี้จะใช้เวลา แต่ผลลัพธ์ที่ได้ถือว่าเกิดประโยชน์ด้านต้นทุนและเพิ่มผลผลิตอย่างมีนัยสำคัญ
●
|
เพิ่มกำลังการผลิตโดยเพิ่มจำนวนชิ้นงานที่ออกมาแต่ละครั้งของการพันคอยล์
|
●
|
ลดต้นทุนขั้นต้น
|
●
|
ลดพื้นที่การใช้งาน
|
●
|
การใช้เวลาเตรียมงานนานเกินไป
|
●
|
ปรับปรุงความซับซ้อนและความเที่ยงตรงของ Jig
|
●
|
มีขีดจำกัดด้านลักษณะรูปร่างและสเป็คของชิ้นงานที่จะรองรับได้
|
|
▲ PAGE TOP
ควบคุมคุณภาพให้มีเสถียรภาพโดยพัฒนาเครื่องจักรบัดกรีอัตโนมัติ
(ลดปัญหา Solder ball ปรับปรุงให้งานด้านการบัดกรีเสถียร)
|
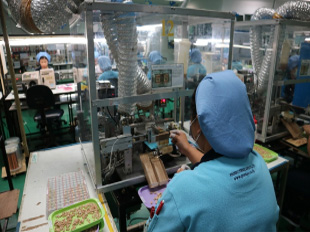
|
เพื่อควบคุมปัญหา Solder ballที่มีขนาดเล็กระดับ 10 ไมครอน บริษัทฯได้ปรับปรุงเครื่องบัดกรีอัตโนมัติ (Rotary type, Arm Type) โดยสามารถป้องกันการฟุ้งกระจายของSolder Ball ทำให้เกิดเสถียรภาพด้านคุณภาพ โดยนำปัญหาในอดีตมากำหนดมาตรการปรับปรุงแก้ไขปัญหาSolder ball
●
|
ลดเวลาการทำงานและการตรวจสอบ
|
●
|
ทำให้เกิดความเสถียรในการบัดกรี
|
●
|
ปรับปรุงระดับงานดี(Yield)
|
●
|
จำเป็นต้องปรับเปลี่ยนบางส่วนตามผลิตภัณฑ์กลุ่มเป้าหมาย
(เกิดต้นทุนขั้นต้น)
|
●
|
เหมาะสำหรับการผลิตจำนวนมาก (200 Kpcs ต่อเดือน)
|
|
▲ PAGE TOP