We would like to introduce at the actual case examples, such as individual customizations and customer feedback.
Improvement of quality management by automated system introduced recording, calculation, and analysis
|
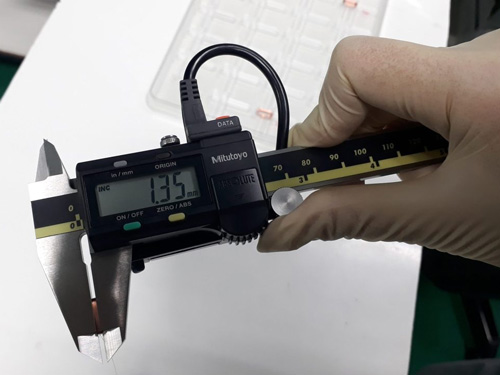
|
We have introduced an automatic measurement software called QC Pro, which reflects the customer feedback that it is difficult to write and read when preparing an inspection data by hand. This improvement much reduced the time required to make the coil inspection data and improved quality management.
●
|
Improvement of quality management
|
●
|
Easy-to-trace management with search capabilities
|
●
|
Provide correct Inspection data to customers
|
●
|
Periodic inspection of the system is required
|
|
▲ PAGE TOP
The quality stabilization through integrated production system (Overmolded coil)
|
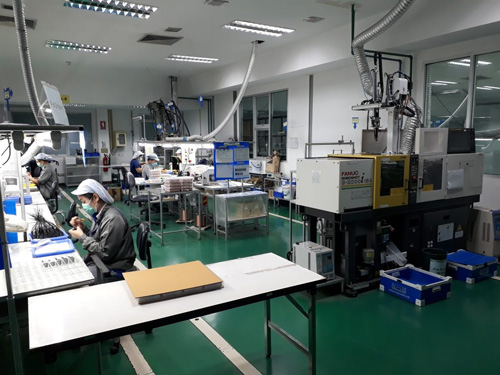
|
We have achieved quality stabilization by build the integrated production system for products that have been distributed to several companies in each process.
Based on a general-purpose winding machine, each part is modified to adjust the tact balance of each process, and then the molding, winding, assembly, and overmolding processes are integrated into a single line, greatly improving productivity while suppressing in-process inventory.
●
|
Stabilization of process and quality
|
●
|
Clarify responsibility in the event of trouble, and speed up investigation and action
|
●
|
Shorter delivery times
|
|
▲ PAGE TOP
Improvement of production capacity by multiple spindle and multi-cavity 2nd winding
|
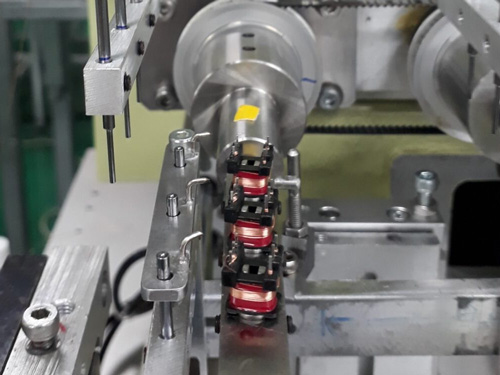
|
In order to meet the increase in customer demand, PRONEC much improved production capacity from 150Kpc/month to 300Kpc/month by multiple spindle and multi-cavity of the 2nd winding processes of small transformers manufactured with single-axis winder.
This improvement has produced us to respond to requests for increased production without adding operator to the production line.
●
|
Improved production capacity
|
●
|
Reduce defects by improving bobbin accuracy of position
|
●
|
Improved quality by reducing manual labor by operator
|
●
|
Increase in preparation time when resumption of production
|
|
▲ PAGE TOP
Improvement of work efficiency of characteristic inspection and test process
|
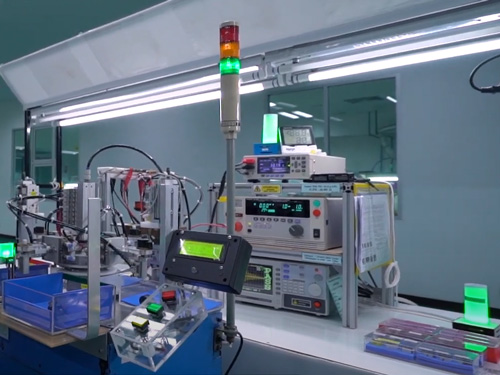
|
In order to meet the increase in customer demand, we have worked to improve the efficiency of the characteristic inspection and test process. Previously, four inspection and test processes were carried out separately: resistance inspection, withstand voltage test, insulation resistance test, impulse test, but the work efficiency was greatly improved by making probes common, switching inspection machines, and even move products. If the measurement result is OK, the product is automatically move, and if it is NG, it is controlled to be move to a special box.
●
|
Improved production capacity
|
●
|
Prevention of variability in measurement conditions by manual operation
|
●
|
Prevention of visual oversight of inspection results
|
●
|
Periodic inspection of the entire system is required
|
●
|
There is a limit to the shape of the product that can be applied
|
|
▲ PAGE TOP
Improvement of production capacity by multiple spindle winding
|
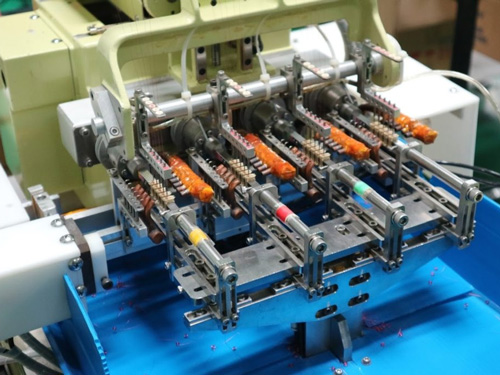
|
In order to reliably mass-produce millions of products a month at a low initial cost, we have improved in-house a multiple spindle winding, which usually produces one winding on one spindle, and have achieved a large number of one spindle 5pcs. It took six months to stabilize the quality, but the production capacity of each equipment has improved dramatically.
This method of production increases preparation time in exchange for production capacity, but provides significant cost benefits when there is more than a certain number of production volumes.
●
|
Increase production capacity by increasing the number of getting
|
●
|
Reduce initial cost
|
●
|
Reduced space
|
●
|
Increasing setup time
|
●
|
Complexity and high-precision of jigs
|
●
|
There is a limit to the shape of the product that can be applied
|
|
▲ PAGE TOP
Quality stabilization through in-house automatic soldering machine (reduction of solder balls, stabilization of solder level)
|
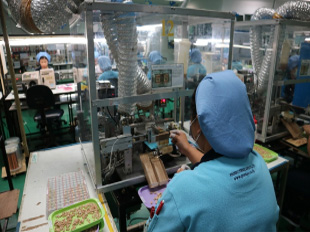
|
In order to control solder level in tens of microns and prevent solder ball scattering, automatic soldering machine (rotary type, arm type) has been developed to achieve quality stabilization. By incorporating all possible countermeasures against defects based on past performance, the scattering of solder balls is reduced.
●
|
Stabilization of solder quality
|
●
|
Reduction of work and inspection processes
|
●
|
Improved yield
|
●
|
Partial modification is required for the target product (initial cost is incurred)
|
●
|
Suitable for mass production (Monthly production 200Kpc~)
|
|
▲ PAGE TOP