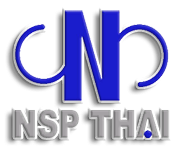
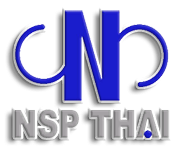
NISSAN SPRING (THAILAND) CO.,LTD.
Challenge to Top Precision Spring Company in ASIA
Our KAIZEN (Improvement) activities from Q.C.D. viewpoint
The number of employees' suggestion for KAIZEN activities have been increasing year by year since its start. The number of suggestion which used to be only a few monthly at the beginning is now more than 50 always. At the morning assembly beginning of every month, we give an award to the employee who made a best suggestion. Other than monthly activities, we hold KAIZEN contest twice a year where 14 teams compete each other for the championship. The champion team is also awarded by overall score. | ![]() |
![]() |
・Seiri |
![]() |
【BEFORE】 We air-blow the power dust adhere to the gap of springs after chamfering by dry barrel. It had taken more than 1 minute for complete removal. |
![]() |
【BEFORE】 Setup operator used to set up by reading the setup manual sheet in which the arrangement was closely described. |
![]() |
【BEFORE】 Improper labeling occurred infrequently in the past, and it had taken time and effort to figure out WIP and inventory. |