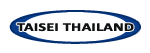
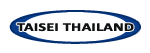
TAISEI KOGYO (THAILAND) CO.,LTD.
金属粉末射出成形(MIM)部品の製造・販売
技術紹介 |
■金属粉末射出成形(MIM)法
金属粉末射出成形法(Metal injection moulding, MIM)の工程概略図です。MIMは、樹脂、ワックスなどからなるバインダーと金属粉末を混錬したフィードストックと呼ばれる材料を使用します。このフィードストックを部品の最終形状を加工した金型に射出成形することで成形体を作製し、この成形体を脱脂・焼結し金属製品を製造します。
■他工法との特性比較
各工法の生産性と形状を比較した図です。MIMは一般的に形状自由度が高く、かつ生産数量の多い金属部品の製造に適していますが、我々のμ-MIM®技術はさらに形状自由度を高めた形状の金属部品を安定した品質で量産します。
■取り扱い材料MIMは、一般的な粉末冶金同様、難削材や高融点金属などの加工に優れています。しかしフィードストックの開発と、微細で球形の粉末を使用する必要があるため、材料選択肢が他の粉末冶金法、例えば圧粉成形品に比べると少ない傾向にあります。 しかし、我々のμ-MIM®は、フィードストックの開発から対応するため、MIM業界の中でも対応できる材料選択肢が多く、他MIMメーカーでは対応が難しい銅も取り扱っています。 |
|
■一般的なMIMとμ-MIM®の違い
特に微小で複雑な形状を持つ金属部品の量産に特化している我々のμ-MIM®の特徴を表にまとめました。
焼結上がり品の寸法精度、焼結密度、薄肉形状などの微細形状に優位性があります。
μ-MIM® | 一般的なMIM | |
寸法公差 (mm)
基準寸法5mm以下の場合 | ±0.01 | ±0.03 |
相対密度 (%) | >98.5 | 95 - 98 |
最小肉厚 (mm) | 0.1 (< 5 mm角) | 0.3 (部分的) |
■形状自由度を高める3D-μMIM技術
3D-μMIMの工程概略図です。他工法、あるいは一般的なMIMでは離型出来ないような形状を、安定した品質で量産する技術です。
図のような曲面を持つ内部構造、アンダーカットがある形状は一般的な加工法では量産が困難です。3D-μMIMはさらに複雑な曲線分岐流路や離型が難しい微小な部品の量産に実績があります。
■3.5D Printing技術が試作検討期間を短縮これまで培ったμ-MIM®技術を活かした、金属3Dプリンティングの進化版である、3.5D Printing技術が新しく我々の技術リストに加わりました。 写真は新たに導入した、リソグラフィー技術で3次元構造を作製するプリンターです。 μ-MIM®が得意とする微細構造を高精度に製造し、試作にかかる納期と費用を大幅に削減します。成形体の作製工程が異なるのみで、その後の脱脂、焼結工程はμ-MIM®技術を応用するため、試作期間後の量産に移行する差異の技術障壁を限りなく小さくします。 |
![]() |
■μ-MIM®の領域
一般的なMIMが得意とする領域と、μ-MIM®が得意とする領域を部品のサイズと要求される寸法精度を軸に示した図です。
μ-MIM®はこれまでのMIMが担ってきた領域、常識を覆すサイズ、寸法精度を安定した品質で実現します。